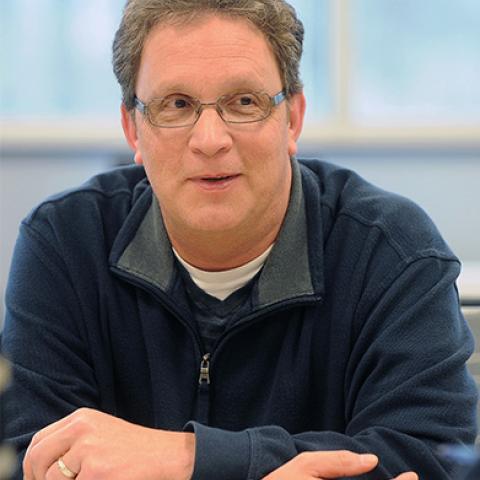
Lean Problem Solving
Problems exist in all organizations. In the fast-paced and high-stress levels of today鈥檚 professional environments, the ability to solve problems quickly and effectively is an essential skill. In this program, participants will learn a simple but proven step-by-step approach for attacking and solving problems. Within the time-honored Plan-Do-Check-Act (PDCA) framework, participants will learn how to develop a standardized, yet flexible process that integrates easily into any current company format.
To prepare for this program, participants will be asked to bring a simple, real-life problem to work on as they utilize the practical tools and techniques of PDCA in a series of hands-on exercise.
- Identify Problems and Write Effective Problem Statements
- Apply the PDCA Problem Solving Process
- Get Past Symptoms to Root Cause and Discover Solutions Using Tools, such as:
- Process maps
- Pareto diagrams
- 5 whys
- Cause-and-affect (fishbone) diagrams
- Standard work
- Facilitating Team Meetings: The Basics
- Develop and Use A3 Reports to Detail and Communicate the Results of the PDCA Process
- Sustain Problem Solving at all Levels and Begin to Create a Continuous Improvement Culture
This eight-hour program is targeted for all associates that serve on problem solving teams.
We can tailor this program and deliver it on-site for your employees and leaders.
Facilitator

John Potkalitsky retired from Eaton Corporation after 20 years of successfully providing hands-on leadership in Lean transformation activities for manufacturing and office environments at both domestic and international plant sites
鈥淚t was a good program that got its meaning across in a very active and engaging way.鈥
Sean Bragg, Plastic Extrusion Operator 鈥淎鈥,
Trelleborg